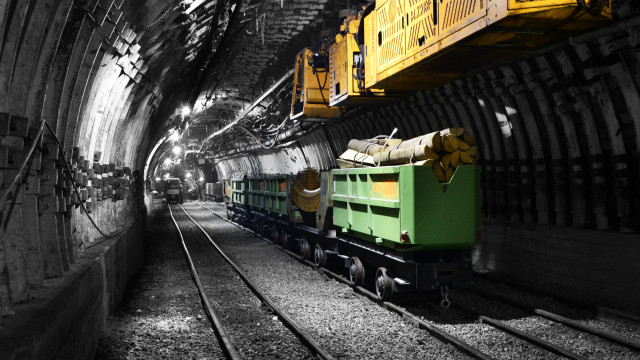
This article outlines some common problems encountered in deep mines, and how optimised transport systems can help solve them.
From recognising day-to-day issues for miners and areas where costs can become unnecessarily high, to identifying the causes of lower workplace performance and the risk of accidents within mines, this article looks to answer many questions that are commonly held by mining companies.
ENSURING THE SUPPLY OF MATERIALS TO THE MINE’S WORKPLACES
A timely supply of excavation and reinforcement materials is crucial for maintaining trouble-free operations and cost efficiency in your mining operation. An insufficient supply of these materials can negatively affect the progress of the mining operation, leading to delays and downtimes that ultimately result in cost increases.
This holds true for every phase of the mining project. From the earliest mine-building activities, through to when activity progresses to the mining face and during subsequent phases of continuous excavation, the timely supply of materials required for excavation and reinforcement is always needed. The supply of excavation technology, or various negative influences such as geological disturbances, high water inflows or the release of gases, may be excluded from this.
For optimised transport of materials in, out and within the mine, we provide an accurate overview of how many transport units work in the mine and where they are located at all times. Since all movement of material is monitored online at the dispatching station, the dispatcher who controls transport always has accurate, up-to-date information about material loads. This information includes what and how much material is on the way from the central warehouse to the destination, an overview of the stock of required material at each mining site, and how much stock of the materials are located at the mining transshipment depots.
Material stocks in the central warehouse are also monitored and managed. The dispatching station plans rides for individual transport units that are fully integrated with the complete transport planning in the mine. High efficiency of all transportation in your mine is ensured and operating costs reduced as much as possible.
OPTIMISING THE TRANSPORT OF PEOPLE TO THE MINE’S WORKPLACES
The most efficient mining operations ensure that miners get to their workplace as quickly as possible. Unfortunately, it is not uncommon for miners to have to walk for several kilometers before reaching their stations. Then, they’ll have to walk all the way back again at the end of their shift. This can take up valuable time for each miner.
Why does this happen? Because often mines use only a limited number of low-capacity wheeled transport vehicles that aren’t able to transport hundreds of miners to workplaces that may be several kilometers away from a vertical pit, or the entrance to a sink hole.
This problem is not solved by acquiring more wheeled vehicles in order to transport more miners. Doing so would increase traffic density inside the mine, contribute to higher levels of air pollution, add unnecessary noise pollution to the working environment, and increase the likelihood of accidents. In addition, acquiring more vehicles would further increase the cost of operating and maintaining the fleet overall.
A Ferrit monorail system can solve many of these problems. It’s high-capacity personnel cabins can transport miners to their workplaces faster and more safely than wheeled vehicles can. Traffic density inside the mine is reduced, firstly because the transportation is suspended and secondly because it is carefully planned and monitored, both for short and long distances. As the monorail is powered by electricity, pollutants are non-existent and noise levels are kept to a minimum.
COORDINATING MATERIAL DELIVERY WITH THE MINE’S MAIN TRANSPORT PROCESS
Transporting materials from the mine’s surface to workplaces inside the mine – whether it’s from face advances, transship points, warehouses or mining deposits – isn’t often treated as a particularly important process, or one that should be kept short.
Instead, material destined for workplaces often gets lumped together with other material due to be imported or exported from the mine. If the supplied material isn’t transported correctly, or if it isn’t stored in the correct container and used straight away, it can build up on the ground at workplaces where it can deteriorate or get damaged. Again, this contributes to rising operational costs when damaged material needs to be replaced.
By selecting the right handling and transport options to and from your workplaces, we help to drastically increase the efficiency of your overall material handling and transport process. We also promise to significantly increase levels of safety for your miners when they handle material. Ultimately, our consistent material consumption planning will help you to better manage your mine’s operating costs.
Optimize your transport system and reduce costs by contacting us today at +420 778 491 237 or [email protected] to arrange a meeting with our sales representative or request more information.