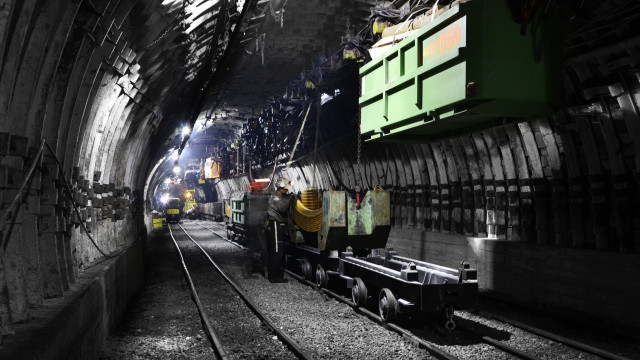
Concluding our three-part series focussing on mining transport, we take a closer look at how the proper handling of mining material ensures maximum efficiency, safety and security during transport, while contributing to a noticeable reduction in operational costs.
In an optimised transport process, material should only be loaded and unloaded once – at the beginning of the process, in the mine’s central warehouse, and at the mining workplace for which it is intended.
PROPERLY HANDLING MINING MATERIAL DURING THE TRANSPORT PROCESS
During the transport process, there should be no transfer of material from one mode of transport to another. If it becomes necessary for material to be transferred several times as it’s moved from warehouses on the surface to workplaces within the mine – if it needs to be removed from its transport and reloaded, or stored somewhere outside temporarily, for example – then overall the transport process becomes extremely costly.
In addition, there is a higher probability that material will be lost during transport or mechanically damaged if the material is handled manually. The risk of accidents also increases. In the end, the entire transport process becomes highly inefficient and economically unfeasible.
At FERRIT, logistics planning is our strong specialisation. We thoroughly analyse and map out all parameters of your transport process, from both raw and support materials logistics to transport routes and the locations of warehouses, workforces and workplaces. We then propose a solution that combines the most appropriate transport equipment, coordination of dispatching, inventory management and containerisation to ensure that transport sets are properly filled, and that no empty trips are made.
Due to these measures, manual handling of materials is kept at an absolute minimum, preventing the extent of material losses and damage, while the number of transport trips made is reduced, which reduces the risk of accidents taking place.
CHOOSING SUITABLE TRANSPORT FOR RELOCATION OF THE MINE LONGWALL
Many coal mines typically carry out wall mining. With this method, all machinery, including mine harvesters, scraper conveyors, sections of mechanised reinforcement and other equipment, must be moved to a new mining face after the wall has been extracted.
Managing this relocation with the help of wheeled transport and LHD vehicles can often take several months. Meanwhile, the use of heavy load bearing railed transport sets can help to reduce timings by a third. In this example, the well-known phrase of “time is money” holds completely true. The sooner the face is cleared, the sooner mining on the new face can start.
With the use of FERRIT’s extreme load bearing and modular monorail system, construction of the monorail track follows the progress of the longwall. The transport of people, raw materials and support materials to the constantly moving face is therefore faster, more convenient and more cost efficient.
MANAGING THE TECHNICAL SECURITY OF MATERIAL
Proper and fully functioning transport systems in deep mines must be connected closely with the process used to control the technical security of material. Failing to properly manage a mine’s inventory will result in disruption to the supply of materials at mining workplaces, which in turn contributes to worker downtime and financial losses for the mine’s owner.
FERRIT transport and logistics specialists carefully study your unique mining operation to create a custom designed system of material management. Our experts define specific zones in your mine, even taking care to create a method of labelling and registering material in your enterprise software system, such as SAP software. All these measures contribute to ensuring the full technical security of your material.
SPECIALISING IN OPTIMISED TRANSPORT SYSTEMS FOR DEEP MINES
The scenarios included in this three-part series have provided just a few examples of areas where we use our expert knowledge to improve the transport of people, material and all mining equipment at either inclined or horizontal mining operations.
For almost 30 years, we have specialised in offering tailored, comprehensive transport solutions for a variety of mining environments, from vertical pits to inclined mine shafts, high risk operations with gas or dust explosions, low profile mines and highly aggressive mines to ensure smooth and efficient mining operations, at the lowest possible costs.
Our goal and promise for every mining project is two-fold. Firstly, it’s about designing a customised transport system that brings you a significant increase in transport efficiency, a reduction in operating costs and a boost to workplace safety. The second goal is to ensure you receive a full return on your investment within two years, due to the significant reduction in operating costs that its solutions provide.
Contact us today at [email protected] or +420 778 491 237 to arrange a meeting with our knowledgeable sales representative or request more information about how we can help you reduce costs with tailored transport and logistic solutions.